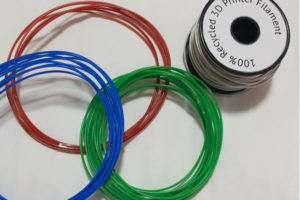
ANZRP is excited to announce its plans to build the world’s first commercial e-waste plastic micro-factory after receiving a $250,000 grant from Sustainability Victoria.
In partnership with UNSW SMaRT Centre and e-recycler TES, the micro-factory will process up to 500,000 kilograms of waste plastic per year. This will be recovered from e-waste recycling and reformed into 3D printer filament for retail sale. Worldwide demand for plastic 3D printer filament is estimated to triple during the next four years, reaching a value of more than USD$1,965.30 million by 2023[1].
With the upcoming e-waste ban in Victoria and growing restrictions on exports of mixed e-waste plastic, options to reduce the cost of recycling and keep these materials out of landfill are important. This project aims to reform a waste stream (e-waste plastic) that’s currently shipped overseas for processing.
“The e-waste plastic micro-factory is a truly circular economy approach that ensures materials are kept in productive use,” says ANZRP CEO, Warren Overton.
“We’re so pleased to be supporting Australian innovation from UNSW and TES that helps improve e-waste recycling.
“As the volume of e-waste continues to increase, technologically advanced approaches such as micro-factories will play a key role mitigating the impact of old televisions and computers.
“By working alongside industry and internationally recognised research hubs, ANZRP is committed to ensuring all e-waste is managed responsibly. This reduces environmental impact and creates employment.”
Victorian Minister for Energy, Environment and Climate, Lily D’Ambrosio says, “These grants will help develop a circular economy that maximises the reuse of materials and reduces the amount of waste that goes to landfill. These exciting projects across Victoria will stop waste, boost the resource recovery industry and create jobs.”
With construction due to start early next year, the micro-factory will be housed at the TES e-waste recycling facility in Somerton, Victoria. This portable factory has the potential to be moved and process recovered e-waste plastic in other areas.
“The micro-factory has the potential to scale and accommodate the 6,000-tonne plastic feedstock that is currently produced each year from the e-waste recycled through the TechCollect program. We have taken the first step with a scalable solution that has guaranteed feedstock, strong environmental benefits, as well as economic benefits through the creation of employment opportunities in regional and metropolitan parts of Australia,” concludes Warren Overton.
[1] 3D Printing Plastics Market by Type (Photo polymer, ABS, Poly amide, PLA), Form (Filament, Liquid/Ink, Powder), End-Use Industry (Healthcare, Aerospace & Defense, Automotive, Electrical & Electronics), Application, and Region – Global Forecast to 2023, MarketsandMarkets